Comprehensive Review of E6000 High Viscosity Adhesive
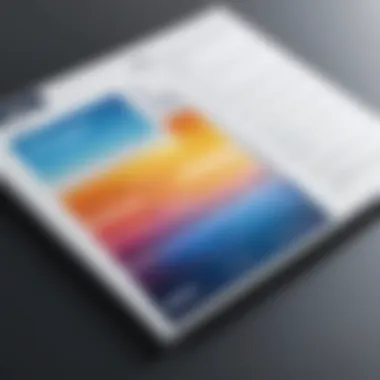
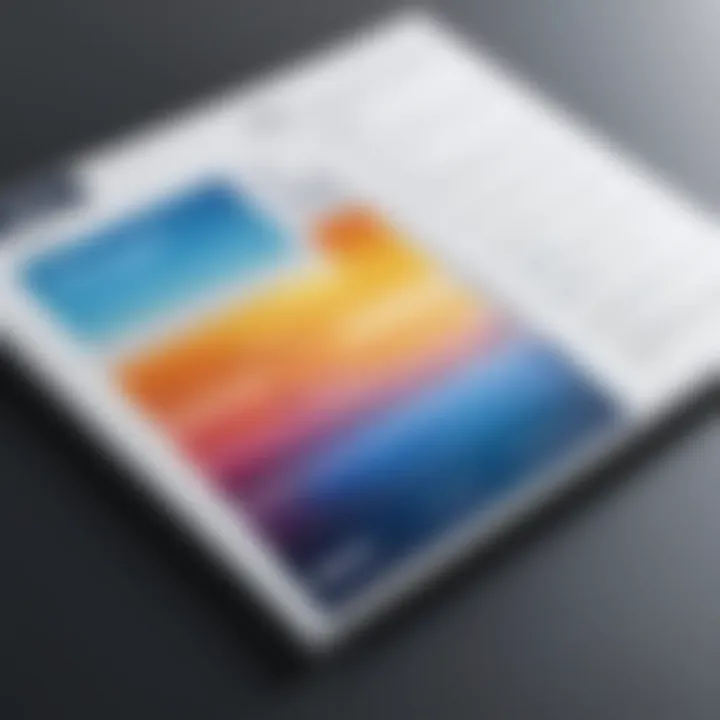
Intro
E6000 high viscosity adhesive stands as a formidable choice in the world of adhesives, particularly appealing to tech enthusiasts and DIY builders. With a balance of strength and flexibility, this adhesive is used in various applications ranging from crafting to industrial uses. It offers a reliable solution for projects requiring durability and resistance against harsh conditions. The focus of this analysis will be to dissect its unique properties, performance metrics, and advantages over competing products. This will ultimately aid users in making informed decisions when selecting an adhesive for their specific needs.
Product Overview
Brief Description
E6000 is a multi-purpose adhesive recognized for its high viscosity formulation. It cures to form a strong, flexible bond that is resistant to moisture, chemicals, and temperature fluctuations. Its versatility makes it suitable for both indoor and outdoor applications.
Key Features
- High Viscosity: This feature allows E6000 to be applied easily on vertical surfaces without running.
- Flexible Bonding: Once cured, it maintains flexibility, making it applicable to materials that are subject to movement.
- Moisture and Chemical Resistance: This property ensures that the bond remains intact even in adverse conditions.
- Transparent Finish: It dries clear, making it ideal for projects where aesthetics are important.
Available Variants
E6000 is available in various package sizes and configurations. Options include small tubes for light projects and larger containers suitable for extensive applications. Users can choose the variant that best fits their project scope.
Specifications Breakdown
Technical Specifications
- Base Material: Synthetic rubber
- Color: Clear
- Curing Time: Approximately 24 hours to reach full strength
- Temperature Range: Effective in temperatures from -40°F to 200°F (-40°C to 93°C)
Performance Metrics
E6000 exhibits a peel strength of around 20 pounds per inch, showcasing its excellent adhesion capabilities. A tensile strength of 80 psi allows it to withstand significant force without failing.
Compatibility Information
E6000 bonds well with a wide range of materials, including:
- Wood
- Metal
- Glass
- Ceramics
- Fabrics
Comparative Analysis
Competing Products
Several alternatives exist in the market such as Gorilla Glue, Loctite, and Aleene's Original Tacky Glue. Each has its unique strengths and weaknesses in comparison to E6000.
Strengths and Weaknesses
- Strengths: E6000's high viscosity is a significant advantage for vertical applications. Its flexibility and weather resistance are also commendable.
- Weaknesses: It requires a longer curing time compared to some fast-setting adhesives. The application can be messy if not handled carefully.
Price Comparison
E6000 generally falls within a competitive price range when compared to similar products. Users often find that the performance justifies its cost, especially for demanding applications.
Buying Guide
Target User Profiles
E6000 is ideal for:
- Hobbyists and crafters
- Electronics builders
- Repair technicians
Important Considerations
Before making a purchase, consider the following:
- Project Requirement: Assess whether the flexibility and curing time fits your specific needs.
- Material Compatibility: Ensure the adhesive is suitable for the materials involved in your project.
Insider Tips for Buyers
- Check local craft and hardware stores for availability; some variants might only be found online.
- Examine user reviews for real-world performance insights.
Maintenance and Upgrade Insights
Regular Maintenance Practices
Although E6000 is designed for durability, proper application can enhance longevity:
- Avoid exposure to direct sunlight during the curing phase.
- Store properly in a cool, dry place to maintain adhesive quality.
Upgrade Paths and Options
For those seeking enhanced performance, consider using E6000 with surface preparation techniques or primers designed for specific materials.
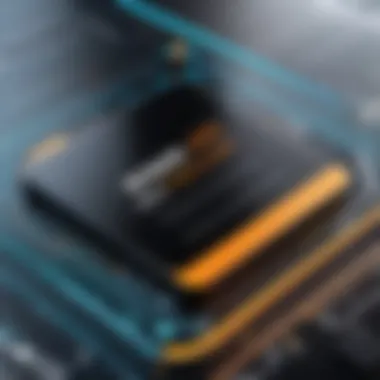
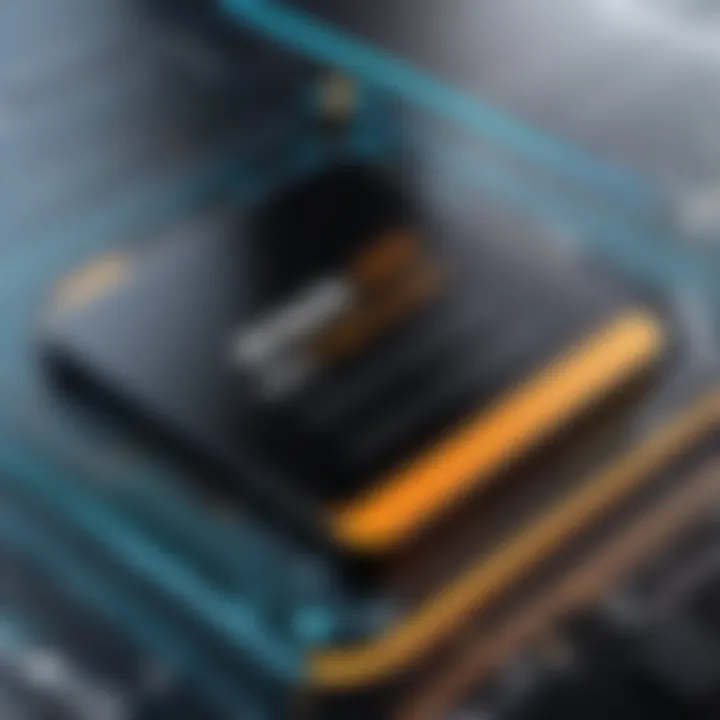
Troubleshooting Common Issues
- If the bond breaks: Ensure surfaces were clean and dry before application. Inadequate surface preparation can lead to failures.
- For bubbling during curing: This can occur if the adhesive is applied too thickly. A thinner application or adjusting the environment can help.
Understanding E6000's capabilities equips users with the necessary insights to maximize its potential in various applications.
Prelude to E6000 High Viscosity Adhesive
E6000 high viscosity adhesive stands out in the realm of adhesives thanks to its unique properties and diverse applications. It is vital for both tech enthusiasts and DIY builders to understand this adhesive, as it offers practical solutions for various projects. From crafting to electronic repairs, E6000 plays a significant role in achieving durability and reliability in bond strength.
Overview of Adhesives in Technology
Adhesives are crucial in multiple fields, particularly in technology. Their primary function is to attach materials together without mechanical fasteners. This is especially important for electronic devices, where space is a constraint and weight reduction is a priority. Various types of adhesives exist, including cyanoacrylates, epoxies, and hot melts. Each type has its specific advantages, influenced by factors like temperature resistance and bonding strength.
Understanding these distinctions can help users select the right adhesive for their needs. E6000's unique formulation allows it to excel in many environments, making it a favored choice among professionals and hobbyists alike.
What is E6000 Adhesive?
E6000 adhesive is a high viscosity, industrial-strength adhesive. It is primarily composed of a combination of polyurethane and a proprietary silicone blend. This gives E6000 its impressive flexibility along with excellent strength. Its viscosity allows for controlled application, making it ideal for small, intricate projects as well as larger jobs.
When applied, E6000 cures to form a strong, waterproof bond. This quality makes it suitable for various materials, including wood, fabric, metal, ceramic, and glass. Users appreciate its durability, which remains effective in extreme conditions and temperatures. This versatility, combined with its user-friendly application, enhances its popularity among those engaged in various types of crafting and repair projects.
Creativity in application can unleash new potentials; E6000 provides a pathway to innovative solutions.
Understanding E6000 adhesive not only reveals its benefits but also emphasizes the importance of choosing the right adhesive for specific tasks. As we explore more aspects of E6000 in subsequent sections, the comprehensive knowledge of its properties, applications, and best practices will further empower users in their projects.
Chemical Composition of E6000
Understanding the chemical composition of E6000 is fundamental to grasping its efficacy and applicability. The formulation is a defining characteristic that influences the adhesive's performance, durability, and versatility in various contexts. E6000 is made from a proprietary blend of polyurethane and silicone, which distinguishes it from other adhesives in the market. This combination contributes to its high viscosity and allows it to bond effectively with diverse materials.
The chemical architecture of E6000 also provides insights into its application suitability. Polyurethane is known for its robust mechanical properties, offering excellent resistance to wear and impact. In contrast, silicone enhances flexibility, granting the adhesive the ability to withstand thermal shock and environmental exposure without losing adhesion. The interplay between these components makes E6000 a favored choice among users who require a strong yet adaptable adhesive.
Polyurethane vs.
Silicone Blends
The presence of polyurethane and silicone in E6000 raises the question of functionality: how do these two materials work together? Polyurethane adhesives are often characterized by their high tensile strength and resistance to various stressors. They adhere well to materials like wood, metal, and plastics.
On the other hand, silicone enhances the adhesive’s ability to resist moisture, UV light, and extreme temperatures. This blend results in an adhesive capable of serving multiple roles, such as bonding, sealing, and encapsulating in an array of applications.
Furthermore, the thoughtful integration of these elements contributes to E6000’s viscosity ratings. Users must understand how these characteristics affect the adhesive’s performance in specific projects. For example, in electronics assembly, E6000's unique blend helps minimize damage due to vibrations or temperature fluctuations.
Key Considerations:
- Strength: Polyurethane offers strength, while silicone adds flexibility.
- Environmental Resistance: The blend provides protection against moisture and UV radiation.
- Application Versatility: Suitable for various surfaces and projects.
Understanding Viscosity Ratings
Viscosity ratings are crucial when evaluating an adhesive for a particular task. In the case of E6000, its high viscosity is an essential feature. A higher viscosity rating typically indicates a thicker adhesive that provides a denser film during application. This characteristic allows for better control during application, ensuring that the adhesive does not easily drip or run off vertical surfaces.
Additionally, viscosity affects the adhesive's curing time. A higher viscosity tends to prolong the curing process, allowing for adjustments and repositioning before the adhesive sets completely. This can be particularly advantageous in intricate projects or when precision is required, such as crafting or electronic assembly.
Ultimately, understanding the chemical composition and viscosity of E6000 enables informed choices. When selecting the right adhesive, it's vital to consider the materials being joined and the environmental conditions the final product will face. This knowledge will enhance project outcomes and ensure long-lasting bonds.
Properties of E6000 High Viscosity Adhesive
The properties of E6000 high viscosity adhesive serve as the foundation for its wide application across multiple industries. Understanding these properties is essential for tech enthusiasts, DIY builders, and those involved in electronic projects. These characteristics contribute significantly to the adhesive's performance and usability. E6000's strength, flexibility, and temperature resistance are key factors when evaluating its effectiveness in various contexts.
Strength and Durability
E6000 high viscosity adhesive is well known for its impressive strength and durable bond formation. When cured, it creates a solid structure that can withstand substantial stress and impact. This makes it suitable for both indoor and outdoor use. The adhesion can be observed in different materials, such as metal, glass, wood, and ceramics. Users need to consider the specific application and surface types to gain the maximum benefits.
One notable feature of E6000 is its resistance to water, which helps maintain the integrity of the bond even in moisture-prone environments. However, the exact strength will depend on several factors, including the surfaces being bonded, surface preparation techniques, and curing conditions. When applied correctly, it proves to be a reliable adhesive for long-lasting connections.
Flexibility and Adhesion Characteristics
Flexibility in adhesive materials is crucial, especially in projects involving components that might expand or contract due to temperature changes. E6000 offers a unique combination of flexibility and strong adhesion. The adhesive allows for slight movements between bonded elements without losing its grip. This property is particularly valuable in electronic applications where devices might undergo thermal expansion.
The adhesion characteristics of E6000 are equally noteworthy. It has the ability to form a strong bond even in challenging conditions, such as uneven surfaces or not-so-ideal environments. This is significant for industries that require robust yet adaptable bonding solutions. Whether the task at hand involves crafting models or assembling electronic parts, the flexibility and adhesion characteristics of E6000 play a vital role.
Temperature Resistance
Temperature fluctuations are a real concern in various engineering and crafting applications. E6000 high viscosity adhesive exhibits excellent temperature resistance, allowing it to maintain its bond under different thermal conditions. Typically, it can withstand temperatures ranging from -40°F to 140°F. This versatility allows users to employ E6000 in environments where other adhesives might fail.
By evaluating the temperature range, professionals can choose E6000 with confidence for projects that encounter extreme heat or unforeseen chills. It is especially useful in automotive applications, where parts often experience substantial thermal variations. An understanding of these temperature resistance levels is crucial for achieving desired results in any adhesive project.
Overall, the properties of E6000 high viscosity adhesive — strength, flexibility, and temperature resistance — make it a valuable asset in various applications, empowering users to make informed choices during adhesive selection.
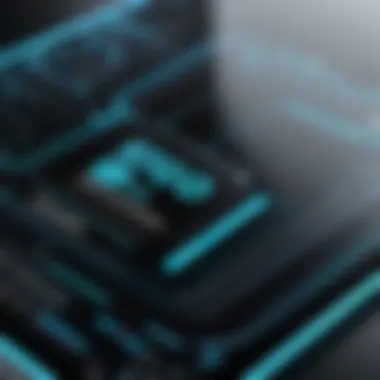
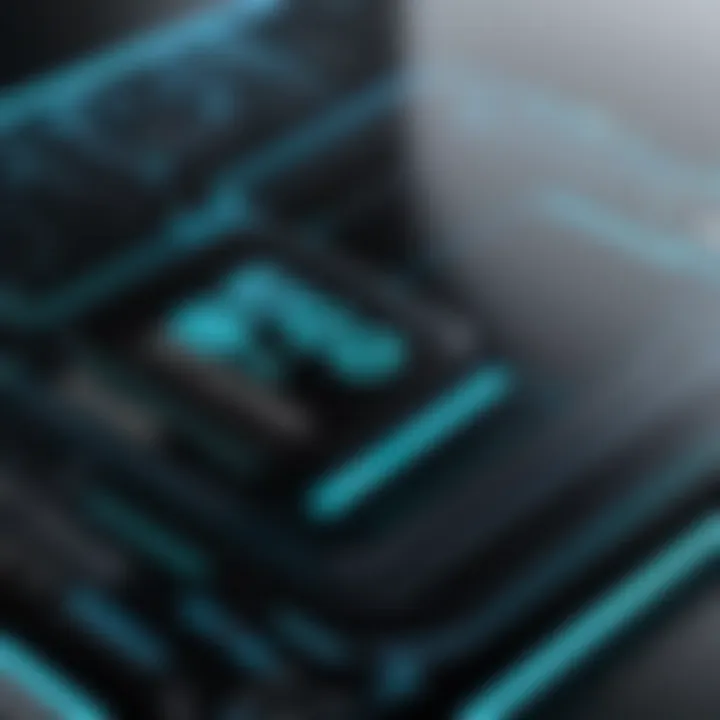
Applications of E6000 Adhesive
The applications of E6000 adhesive are diverse and play a significant role in various industries. Its unique properties make it suitable for a wide range of projects. Understanding these applications is essential for tech enthusiasts, DIY builders, and anyone looking to utilize its advantages effectively. This section will delve into the specific environments where E6000 shines, emphasizing its versatility, strength, and ease of use.
Electronics and Tech Projects
E6000 adhesive is often chosen for electronics and tech projects due to its superior bonding capabilities. Its high viscosity allows for precision application, making it ideal for attaching components where precision is key. For instance, it can be utilized to secure circuit boards, connect sensors, and even reinforce wiring. Unlike some other adhesives, E6000 resists high temperatures and is waterproof, which is critical for electronics exposed to moisture or heat.
Consider the following benefits:
- Excellent adhesion: E6000 adheres well to plastics, metals, and glass, allowing for a wide range of materials to be bonded.
- Flexible bond: This adhesive can withstand stress and movement, which is vital for electronic devices that may experience thermal expansion.
- Fast curing: Though not as quick as hot glue, it provides a reasonably fast cure time that allows for quick project turnaround.
DIY Crafting and Model Making
In the realm of DIY crafting and model making, E6000 adhesive stands out for its versatility. It can handle various materials such as fabric, wood, and ceramics, making it a reliable choice for hobbyists. Models made with E6000 tend to have a strong bond that withstands the test of time, ideal for intricate designs and detailed work.
Key considerations include:
- Diverse material bonding: Whether working with foam, beads, or paper, E6000 excels in creating strong bonds that endure.
- Precision application: The high viscosity allows for controlled dispensing, critical for small or detailed projects.
- Durability: Finished products often exhibit exceptional resistance to wear and tear.
Automotive and Repair Uses
The automotive industry also benefits from E6000 adhesive. It can be used for a variety of tasks, from repairing bumpers to securing trim pieces. The adhesive's resilience to heat and moisture makes it a suitable option in environments where both are prevalent.
Practitioners should note:
- Heat resistance: E6000 withstands higher temperatures found in engine compartments or when exposed to sunlight.
- Strong bond: This ensures repairs remain intact, reducing the need for frequent maintenance.
- Ease of use: Application is straightforward, making it accessible even for those who may not have extensive experience in auto repairs.
E6000 adhesive's ability to bond different materials and resist environmental stresses expands its usage across various sectors, including electronics, crafting, and automotive applications.
Understanding these applications and their advantages assists users in selecting E6000 for suitable projects. By knowing where to apply E6000, DIY enthusiasts and professionals alike can achieve efficient and effective results.
Comparison with Other Adhesives
When discussing the properties and applications of E6000 high viscosity adhesive, it is crucial to compare it with other adhesive types. This analysis will help users understand where E6000 stands among competing options. Each adhesive has unique benefits, limitations, and ideal use cases. Knowing how E6000 interacts with other adhesives makes it easier for tech enthusiasts and DIY builders to make informed choices for their projects.
E6000 vs.
Hot Glue
E6000 and hot glue serve distinct purposes, appealing to different user needs. Hot glue works best for quick, temporary bonds. It sets rapidly when heated but can fail under stress or heat. This makes it less reliable for long-term projects. On the other hand, E6000 forms a strong, flexible bond that withstands various conditions.
Key differences include:
- Bond strength: E6000 typically has superior adhesive strength compared to hot glue, especially on porous surfaces.
- Durability: E6000 is more resistant to water, chemicals, and temperature fluctuations. In contrast, hot glue often loses its grip in humid or hot environments.
- Application: Hot glue guns provide ease of use and quick application for crafting. However, E6000 requires careful application due to its viscous nature, making it more suitable for detailed work.
- Curing time: Hot glue sets within minutes, whereas E6000 needs several hours to cure fully. This longer curing time, however, results in a more durable bond.
In summary, while both adhesives have their merits, the choice between E6000 and hot glue largely depends on project requirements. For temporary, straightforward applications, hot glue excels, whereas for long-lasting solutions, E6000 is preferable.
E6000 vs.
Epoxy Resins
The next comparison involves E6000 and epoxy resins. Both are known for their strong bonding capabilities but cater to slightly different needs and preferences in adhesive applications. Epoxy is often chosen for its unparalleled strength and resistance to harsh conditions, making it an excellent choice for industrial applications. However, E6000 has unique characteristics that may make it a better option for certain projects.
Key considerations include:
- Flexibility: E6000 maintains flexibility even after curing. This attribute allows it to handle vibrations and impacts better than most epoxy resins, which can become brittle over time.
- Ease of use: E6000 is generally easier to apply than epoxy. Users do not need to mix components before use, as is common in most epoxy applications.
- Versatility: While epoxy is often limited to specific materials such as metal and glass, E6000 can bond various surfaces, including fabric, wood, and metal, making it more versatile.
- Curing time: Epoxy adhesives usually require longer curing and setting times than E6000. Some epoxy products can take even longer to achieve full strength, whereas E6000 bonds quickly, allowing for a more efficient working process.
Best Practices for Application
Understanding best practices for applying E6000 high viscosity adhesive is crucial for achieving optimal results in any project. Adhering to specific techniques can enhance the performance of the adhesive, ensuring strong bonds, improved longevity, and the prevention of common issues such as bubbles or misalignment. For tech enthusiasts and DIY builders, employing proper methods not only simplifies the process but also elevates the quality of the final output.
Surface Preparation Techniques
Effective surface preparation is often the unsung hero in successful adhesive application. Surfaces must be clean, dry, and free from contaminants, as any debris can hinder adhesion. Here are key steps to ensure proper preparation:
- Cleaning: Use a suitable cleaner for the surface material. Isopropyl alcohol is often effective, especially for plastic or metal surfaces.
- Sanding: For some materials like wood or certain plastics, light sanding can create a better surface texture for bonding.
- Drying: Ensure surfaces are dry. Moisture can seriously affect the adhesive's performance and curing.
Ultimately, proper preparation can significantly impact the adhesive's ability to hold over time.
Application Tools and Techniques
Choosing the right tools is equally important in the application stage. Proper tools allow for precision, which can lead to neater and more effective results. Some tools and techniques to consider include:
- Applicator Bottle: E6000 typically comes in a tube or bottle. A precision applicator can help control the flow, especially for small details.
- Brushes or Sponges: For larger areas, these can help spread the adhesive evenly.
- Clamps or Weights: Once applied, using clamps can ensure that the surfaces remain in contact as the adhesive cures.
While applying, keep in mind:

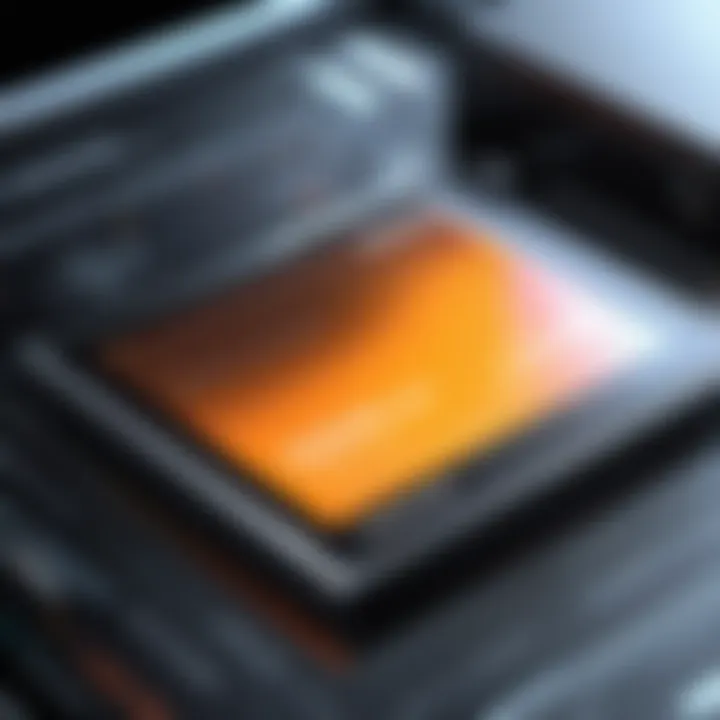
- Apply only a small amount of adhesive; excess can cause mess and longer curing times.
- Ensure even coverage for optimal bond strength.
Curing Time and Conditions
Curing time is a critical phase that must not be overlooked. E6000 requires about 24 to 72 hours to cure completely, depending on conditions and thickness of application. Follow these guidelines to ensure proper curing:
- Temperature: Ideal curing conditions are typically between 70°F to 90°F. Extreme temperatures can alter curing times.
- Humidity: High humidity can help with curing but too much moisture can also lead to improper bonding. Aim for a moderate environment.
- Avoid Movement: Once the adhesive is applied, it is vital to keep the pieces stationary to ensure alignment and bonding strength.
Curing is as important as application; the bond's durability often hinges on this phase. Ignoring it can compromise the overall strength of the adhesive.
By implementing these best practices, users can maximize the performance of E6000 high viscosity adhesive in various applications, ensuring a solid and lasting bond. This systematic approach is particularly valuable for tech projects where precision is paramount.
Safety Considerations
Understanding safety considerations is crucial when working with E6000 high viscosity adhesive. This knowledge helps to prevent accidents and ensures a safer working environment. E6000 emits fumes during its application and curing processes, making awareness of health risks important. Adhering to safety guidelines will benefit even experienced users, as improper handling can lead to various issues.
Health Risks and Precautions
E6000 adhesive contains chemicals that can pose health risks. Inhalation of vapors can lead to respiratory irritations. Skin contact may cause allergic reactions or dermatitis in some individuals. Therefore, it is recommended to:
- Always wear appropriate personal protective equipment (PPE) such as gloves and masks.
- Work in a well-ventilated area to minimize inhalation risk.
- Avoid direct skin contact by using tools or applicators.
If any adverse symptoms arise, seek immediate medical attention. Be sure to read the safety data sheet (SDS) provided by the manufacturer for in-depth health risk information and first aid measures.
Proper Ventilation and Workspace Management
Creating a safe workspace is equally important. Good ventilation reduces the concentration of harmful fumes. Here are practical steps for achieving proper ventilation and workspace management:
- Use exhaust fans if available to increase airflow.
- Open windows or doors to ensure fresh air circulation.
- If working indoors for an extended time, consider a respirator designed for organic vapors.
Additionally, keep your workspace organized and clean. Ensure that other materials that may react with E6000 are stored safely away. Adequate lighting can further enhance safety, allowing users to work more effectively and reduce hazards. Proper management turns potential risks into manageable situations.
Storage and Shelf Life
Understanding the storage and shelf life of E6000 high viscosity adhesive is vital for both professionals and enthusiasts alike. Adhering to correct storage methods directly affects the performance and longevity of the adhesive. This section will cover how to store E6000 properly and what to look for to determine if the adhesive has aged beyond usability.
Optimal Storage Conditions
To maintain the effectiveness of E6000 adhesive, it is important to store it under specific conditions. The following best practices should be observed:
- Temperature: Store the adhesive in a cool area, ideally between 60°F and 80°F (15°C to 27°C). Extreme temperatures can compromise the adhesive's chemical integrity.
- Humidity: High humidity can negatively affect the adhesive. A dry environment helps to preserve its viscosity and overall performance.
- Light Exposure: Keep the adhesive away from direct sunlight. Ultraviolet (UV) rays can initiate chemical changes that lead to degradation.
- Seal Properly: Ensure the container is tightly sealed after each use. Exposure to air can lead to skinning and loss of properties over time.
Following these guidelines will help prolong the adhesive's shelf life, guaranteeing optimal performance when needed.
Signs of Adhesive Aging
It is crucial to recognize the indicators of adhesive aging before application to avoid poor performance. Here are some signs to watch for:
- Separation of Components: If you notice distinct layers or a liquid separation in the adhesive, it may not bond effectively. Shake well, but if it remains separated, consider discarding it.
- Change in Viscosity: A noticeable change in thickness or consistency indicates loss of effectiveness. A very thin texture or an extremely thick consistency is a warning sign.
- Discoloration: Color changes, such as yellowing or darkening, suggest chemical alterations which can hinder performance.
- Odor Changes: A foul or off-putting smell may indicate that the adhesive has spoiled and is no longer safe to use.
Recognizing these signs will help ensure that you only use E6000 adhesive in its optimal state, preserving the integrity of your projects.
By taking care with storage and monitoring the state of the adhesive, you can ensure that E6000 high viscosity adhesive remains a reliable choice for various applications.
Common Use Cases and Examples
E6000 high viscosity adhesive boasts versatility across a variety of applications. Its adaptability makes it especially valuable for tech enthusiasts and DIY builders. Understanding specific use cases and examples can help users maximize its benefits. Knowledge of where and how to apply E6000 can lead to better project outcomes and prevent common pitfalls.
Field Studies and Testimonials
Various field studies support the efficacy of E6000 in real-world applications. Users have reported positive experiences when utilizing this adhesive for electronics, crafts, and repairs.
One notable case involved a group of DIY hobbyists experimenting with E6000 for their homemade gadgets. They found it securely bonded disparate materials like plastic, metal, and glass. Not only did the adhesive perform well under different conditions, but it also offered flexibility, which is critical in electronic components exposed to movement.
Additionally, social media platforms like Reddit have testimonials from builders detailing successful projects. Users often share insights about how E6000 held up over time, noting minimal deterioration compared to other adhesives.
The End
The conclusion serves as a synthesis of the valuable insights gathered throughout the examination of E6000 high viscosity adhesive. This section emphasizes the significance of the adhesive in various applications, underpinning its strengths and adaptability. Understanding E6000's benefits is crucial for users seeking effective solutions for their projects. The adhesive's unusual meshing of versatility and strength makes it a preferred choice in the tech and DIY arenas.
Summary of Key Points
Here is a compact overview of the primary takeaways from the article:
- Chemical Composition: E6000 stands out due to its unique polyurethane and silicone blend, offering a balance between flexibility and durability.
- Properties: Its high viscosity contributes to exceptional strength and adhesion capabilities, ensuring long-lasting bonds in tech builds and craft projects.
- Applications: Ranging from electronics to automotive repairs, E6000's utility is broad, making it suitable for diverse scenarios.
- Safety Tips: Awareness of health risks and adherence to safety protocols enhance user experience and minimize hazards.
- Storage: Proper storage conditions will prolong the shelf life and effectiveness of E6000, ensuring it remains ready for use when needed.
Future Trends in Adhesive Technology
Looking forward, the adhesive industry is poised to evolve significantly. Advances in materials science could lead to the development of adhesives with enhanced performance characteristics and environmental sustainability. Key trends to monitor include:
- Eco-Friendly Formulations: Increasing demand for low-toxicity and biodegradable adhesives is reshaping product offerings in the market.
- Smart Adhesives: Technologies that integrate responsiveness to environmental stimuli, such as temperature changes, are becoming more feasible.
- Enhanced Performance: Research into nanomaterials may lead to adhesives that demonstrate improved strength and flexibility.
These trends highlight the potential for E6000 and similar adhesives to adapt to future needs, ensuring they remain relevant in a rapidly changing technological landscape. Staying informed about these developments can aid users in making informed choices when selecting adhesives for their projects.